Our comprehensive range of repair, maintenance and monitoring services can enhance the performance, reliability and lifetime of nuclear reactor steam turbines.
-
Increased efficiency
-
Improved reliability
-
Higher flexibility
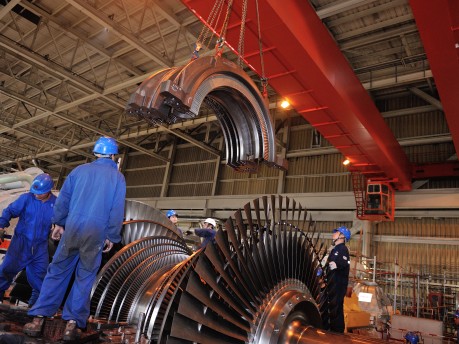
Planned and unplanned outages
Leveraging our extensive installed base, we continuously invest in our steam turbines services solutions to ensure we keep things running.
We repair, monitor and extend the lifecycle of power plants across Europe, Asia and Africa, supporting a wide range of own and other manufacturer’s equipment.
Upgrades
Our expert service team has the technical knowledge to deliver plant equipment upgrades with the latest technology, improving power output, efficiency and reliability. We can customize a solution to increase the output, improve emissions or enhanced operational flexibility.
Retrofits
We have the global experience to replace older components in power plants with modern equipment, extending the lifecycle, reliability and output efficiency. Our team will create customized solutions for your needs.
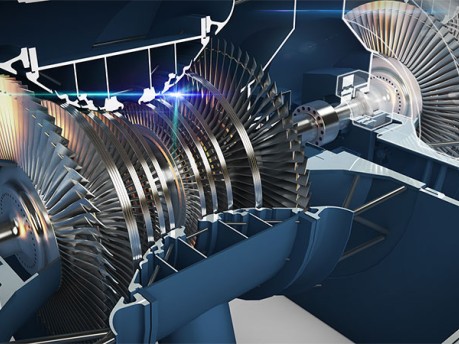
Steam turbine condition monitoring
Our model-based torsional vibration monitoring and diagnostics system offers health monitoring of the turbine’s shaft line for focused outage planning. The advisor enables real-time insight into stresses and vibration amplitudes in all critical locations along the rotor, using a combination of state-of the-art signal processing technology and physical model results.
Permanent monitoring of the torsional vibration helps to assess the potential impact on the fatigue of shafts and components. Unmonitored torsional vibration resonances may lead to a higher risk of rotor cracks in cycling operation modes.
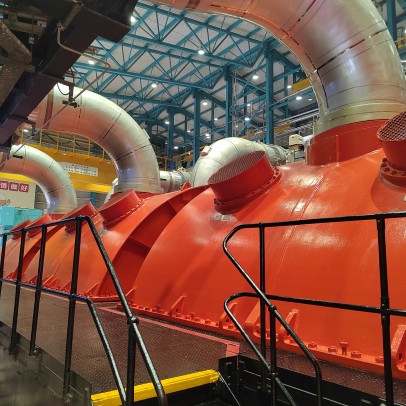
Retrofit delivers power-uplift
After three decades of safe operations, the Daya Bay Nuclear Power Plant in China was seeking to boost the electricity output and extend the operational lifespan of their steam turbines. When it was commissioned in 1994, Daya Bay was the first nuclear power plant using Alstom technology to operate commercially in China.
As a long-term partner the Arabelle Solutions team was tasked with this important modernization project and in 2018 started designing the improved LP module path flow. Manufacturing of the required equipment, including six sets of rotors, inner casings, blade holders and complete bearings, started in July 2020. Despite challenges, including the COVID pandemic and supply chain constraints, the equipment was delivered to the site on time.
The extensive work to retrofit Unit 2 was completed in only three months towards the end of 2023, with successful grid synchronization and testing concluded in early 2024. This was followed by Unit 1, which was retrofitted and passed its stringent tests by the summer of 2024.
Following the retrofit, the modernized plant’s improved effectiveness is expected to save hundreds of thousand tons of CO2 emissions a year, compared to a standard coal powered plant.