We deliver advanced outage planning and execution services for all steam turbine, generator and associated nuclear turbine island equipment.
A strategic partnership approach
Whether you’re dealing with an unplanned outage or operational issue, we understand the importance of getting it right the first time. Arabelle Solutions has the experience to handle both planned maintenance and emergency events requiring speed, from assessing site conditions to getting all the necessary project components and experts in place.
Extensive outage planning experience
-
Mobilization
Field service experts and local craft resource support
-
Executions
Decades of experience with continued investment in services
-
Focus on excellence
Strong focus on quality, safety and on-time delivery
-
Digital solutions
Digital solutions to help better plan for outages and anticipate potential unplanned events
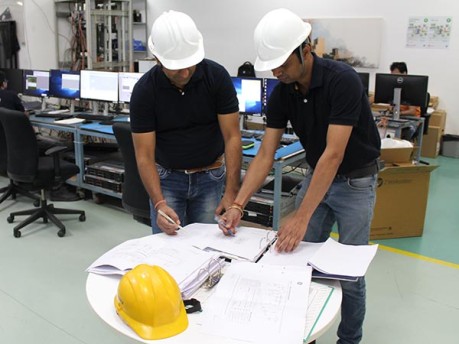
Planning ahead for a successful completion
Our team will work to plant specific requirements for a successful outage execution, taking a partnership approach when developing the schedule. We will explore the maintenance scenarios and identify the important milestones in advance of the outage.
No matter what state of planning or stated objective, Arabelle Solutions has the knowledge, experience and expert engineering teams for an effective outage management.
Power plant outage schedule
Scope: We will work with you to develop a detailed scope of work with clear roles and responsibilities. From standard parts and repair work to steam turbines and generators, all necessary equipment and expected maintenance work will be defined as a team.
Environment, Health & Safety: We will review, support and update site-specific EHS requirements for our teams and the plant outage events to ensure our first priority for a successful safe execution,
Optimization: We have the best practices and expert engineering knowledge as well as the field teams required to plan for an effective outage that addresses the specific objectives. This includes adapting the services scope to reflect the plant's operational characteristics, optimizing the scheduling to fit with the required outage window and other site activities and preparing for potential emergent findings during the planned maintenance.
Parts & tooling kits: Planning is key, for both consumable as well as significant replacement parts with longer lead times. Through our local repair workshops and supplier network, we can engineer or order the required parts. Based on inventory and outage scope, we will start defining what equipment and special tools will be needed for a proper and timely outage execution. From cranes to rotor stands, the tooling kit will be customized to your outage and site.
Scope: We will continue to fine-tune your power plant outage planning through regular touchpoints and transparent communication. Together, we will establish precise mobilization and demobilization plans, including customer training logistics and requirements, site setup, internal and external resource arrival, site turnover, equipment, and tools.
Environment, Health & Safety: Key aspects of EHS include site laydown, lockout & tagout, walk down, delimited storage and quarantine zones. We will discuss and reach an agreement on all these important aspects with you to help ensure a safe plant outage execution.
Optimization: We will consider the planned outage scope as well as potential unplanned activities to define necessary mitigations steps that will help keep your outage on track. Our engineering team will prepare all the necessary technical documentation for our field teams, including field procedures, test protocols and field service instructions.
Parts & tooling kits: This is the time to perform an onsite parts inspection to ensure you have the rights parts at the highest quality. We will work with you to plan the staging and delivery of parts and consumables to meet the scope of your outage.
Scope: We will work together to finalize our communication plan and regular checkpoints, including issue escalation, to remain transparent and allow for quick decision-making on the turbine deck during your plant outage.
Environment, Health & Safety: The team will complete the pre-planning checklist and our regional EHS manager take all aspects of safe outage inspections into consideration. We will conduct briefings for the EHS manager, employees and contractors.
Optimization: Our engineering team will customize the inspection, test plans and review all technical documentation to ensure it fits the site, outage plans requirements.
We will perform all final checks, including parts and tooling kits delivery, to make sure your outage starts on time and is safely conducted.
1 month after outage: Our team will provide a thorough, detailed post-outage report for you, including EHS, delivery time, productivity savings and lessons learned.
2 months after outage: We will organize a post-outage review meeting with you and your team to address any open items, hear about your experience and feed back through the entire organization to continuously improve our performances and processes.
Unplanned outage
Ready 24/7
Unfortunately, not all outages can be planned. From the need for emergency parts, unexpected issue emerging during an outage or even a forced outage, our field teams are ready 365 days a year.
Expert network
Not only can we support last-minute outage requests, we can help you with additional parts from our refurbished part pool. Our team is backed by a global network of technical, repair and analytics experts that can respond quickly to unplanned events.